In the modern dental industry, precision, efficiency and responsiveness are essential to staying competitive. For dental laboratories, collaborating with CAD design suppliers has become a necessity, not only to improve productivity, but also to offer high-quality dental devices that meet demanding industry standards.
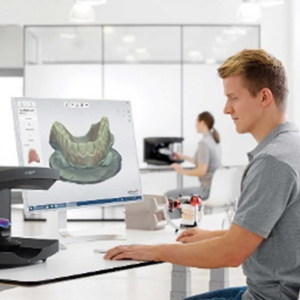
However, one of the key factors that determines the success of this collaboration is the workflow between the laboratory and the CAD design supplier. An optimized workflow can make the difference between timely and accurate delivery, or expensive delays and unnecessary adjustments.
- Efficient communication: the first step towards workflow integration
The basis of any successful workflow between a dental laboratory and its CAD design provider is clear and efficient communication. This goes beyond simple email exchanges; it is about using digital tools that allow real-time interaction, where both teams can share updates and technical specifications without losing details.
The use of collaborative digital platforms, such as Exocad DentalCAD, 3Shape Communicate or Inlab (Dentsply Sirona), is crucial. These platforms allow laboratory technicians to upload clinical case data, such as intraoral scans or digital impressions, directly. The CAD provider can immediately access this data and begin the design, while the laboratory can provide feedback and suggestions in real time, minimizing possible misunderstandings. Agility at this stage of the process ensures that both parties align with the specific expectations and requirements of the case.
- Use of standard formats: ensuring compatibility and accuracy
A vital technical aspect in the workflow is the use of standardized file formats. The STL (Standard Tessellation Language) format is the most commonly used in the dental industry, both for 3D printing and for denture milling. This format allows the precise representation of 3D surfaces, essential for the creation of exact dental devices such as crowns, bridges, or aligners.
Correct STL file management ensures that data transferred between the laboratory and the CAD design provider is compatible with production equipment, such as milling machines and 3D printing systems. Without an adequate and standardized format, adjustment problems may arise, which can result in corrections or even production failures. A well-defined workflow should include a thorough review of these files before moving on to the production phase, to avoid setbacks and ensure that margins, occlusions and other crucial details are kept within the stipulated tolerances.
- Clear role assignment: well-defined technical responsibilities
For the workflow to be efficient, both the laboratory and the CAD design expert company must have clearly defined roles from the beginning. The dental laboratory is responsible for providing the precise data of the clinical case, such as the morphology of the patient, materials to be used and any aesthetic or functional specification. The CAD supplier, for its part, is responsible for translating this data into a digital parametric design, ensuring that each device is faithful to the given specifications and is ready for immediate production.
This division of tasks not only avoids confusion, but also allows each part to focus on its specialty: the laboratory in manufacturing and the CAD supplier in technical design. In this sense, having a clear methodology to review the designs before they go into production is essential to avoid costly errors and ensure that the final product fits perfectly with clinical expectations.
- Review and feedback based on technical parameters
A robust workflow should also include clear review protocols. Before proceeding with the production of dental devices, CAD designs must undergo a technical review that includes the verification of crucial parameters such as adjustment margins, wall thickness, and occlusal analysis. At this stage, feedback from the dental laboratory is vital.
Feedback must be technical and accurate, based on clear metrics. For example, the laboratory may require adjustments in the design of a crown if the thickness of the wall does not meet the production tolerances, or if there are geometric deviations that may compromise the adjustment of the device in the mouth. The use of digital tools that allow these reviews to be carried out in real time significantly reduces waiting times and facilitates a continuous flow between design and production.
- Quality at each stage: ensuring consistent standards
Both the CAD design provider and the dental laboratory must operate under rigorous quality standards. An effective quality protocol ensures that CAD designs are not only accurate, but also viable for their manufacture. Certification under regulations such as ISO 13485, applicable to medical devices, is a good indicator that both teams work under international quality standards.
In practical terms, this means that the digital files produced by the CAD design experts must be optimized for the laboratory’s manufacturing equipment, whether it is a milling machine or a 3D printer. If the designs do not meet the proper technical specifications, the workflow is affected, and the production may face delays or even failures.
- Problem solving: flexibility and adaptability
Even with a well-planned workflow, challenges are inevitable during the collaboration between the dental laboratory and the CAD design provider. However, the key to maintaining efficiency is the ability to solve problems quickly and flexibly. Experts who have advanced tools, with which they can make immediate adjustments without affecting delivery times.
This type of flexibility is essential to ensure that, in the event of last-minute errors or adjustments, the workflow is not interrupted and can be continued without major delays.
- Planning and synchronization: optimization of time and resources
A proper workflow between a dental laboratory and its CAD design provider must be based on precise planning. This involves synchronizing delivery times and ensuring that both teams are coordinated in terms of production times and necessary resources.
With a well-structured workflow, collaboration between dental labs and CAD design providers can optimize productivity, ensure accuracy in end devices, and deliver fast and efficient solutions. For those laboratories that have not yet established a smooth collaboration with experts, this is the time to consider how a good integration can transform their processes.